Roll formed parts & Decorative metal mouldings
OUR SOLUTIONS
In business since 1904.
Dahlstrom Roll Form manufactures OEM metal roll formed parts, as well as decorative metal mouldings for architecture. We provide custom and standard roll formed shapes for both markets.
Our solutions include a huge catalog of made-to-order standard shapes and vendor managed inventory services.
Solidify your supply chain with our:
- 99.5% on-time delivery rate
- Quarterly reviews & forecasting
- Best-in-class PPM defect rate
If you can’t find what you’re looking for in our online catalogs, reach out to us — we’d be happy to discuss options with you.
Roll forming is the process of gradually bending a flat strip of metal into a longitudinal, uniform profile. Roll forming is a cold forming process, meaning that no heat is required to form the metal.
There are clear advantages to roll forming vs. extrusions, stamping, and other metal manufacturing processes. To learn more, visit our Why Partner With a Roll Former page?
From universal OEM profiles to historic decorative metal trim, we’ve got you covered.
Browse our catalogs to see our wide selection of channels, angles, and metal mouldings — from functional to lavish; classic to modern.

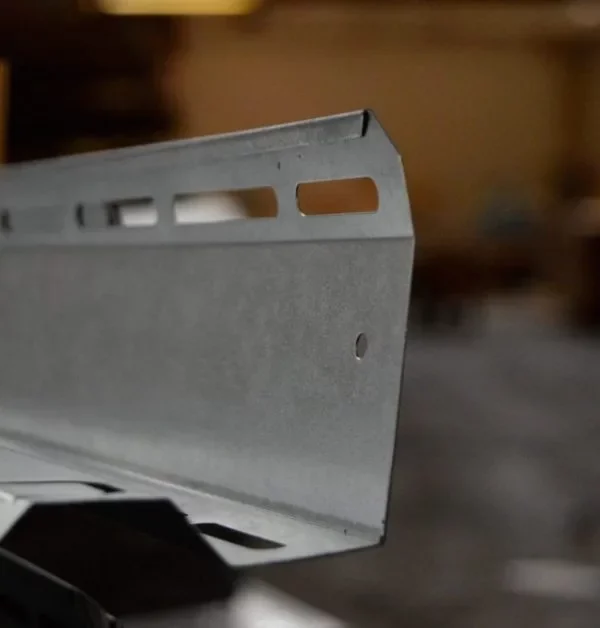
BUY METAL MOULDINGS ONLINE
Visit our eStore for ready-to-ship mouldings. In-stock mouldings ship in less than 4 days.